Jim Timber
5 year old buck +
I decided against building a hydraulic skidding winch after coming to the conclusion that the speed needed wasn't achievable with the desired force out of my hydraulics on the tractor, so I had a motor I wasn't using and decided to build a stump grinder instead. The force generated will be more than adequate for this application, even after speeding up the pumps modest 250 RPM to 1,000 RPM (where most commercial grinders run).
Got lucky at the steel yard a couple weeks ago and found a 21" round 3/4" thick they laser cut out of a plate in the fab shop - .60/lb is a whole bunch better than $1 and having to pay a cut charge and then spend an hour rounding it out of the plate. Score!
Last night I started working on the frame.
Then today I got more material and continued:
They're not visible in the pics, but I have reinforcement bars welded under the latch tabs on the bottom flange. I used 1/4" for this and the bottom flange on my fork carriage, but the forks don't really put much strain on that connection. The grinder will be fighting to get off the QA mount, so I beefed it up a bit more. I'll also be gusseting those pockets from below as well.
Dinner break, and back to it...
Got lucky at the steel yard a couple weeks ago and found a 21" round 3/4" thick they laser cut out of a plate in the fab shop - .60/lb is a whole bunch better than $1 and having to pay a cut charge and then spend an hour rounding it out of the plate. Score!
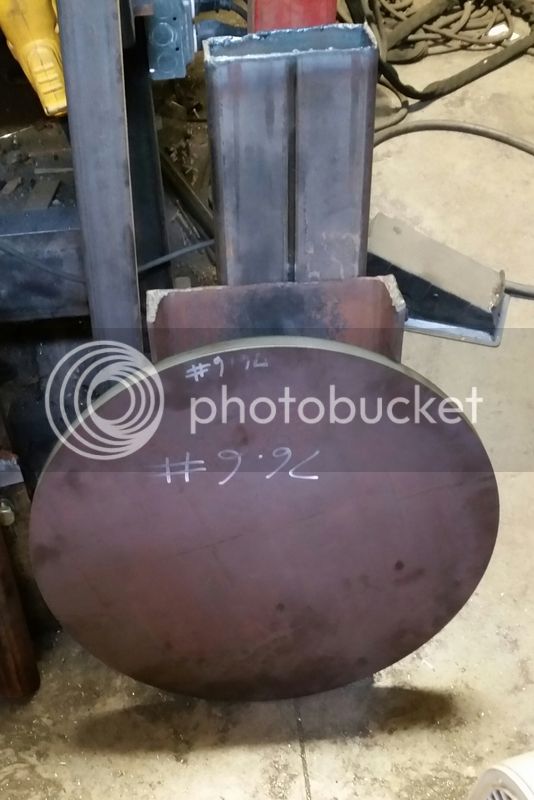
Last night I started working on the frame.
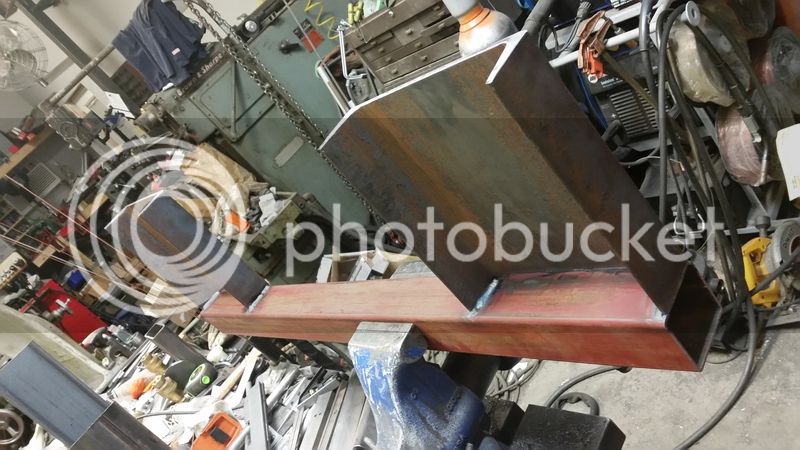
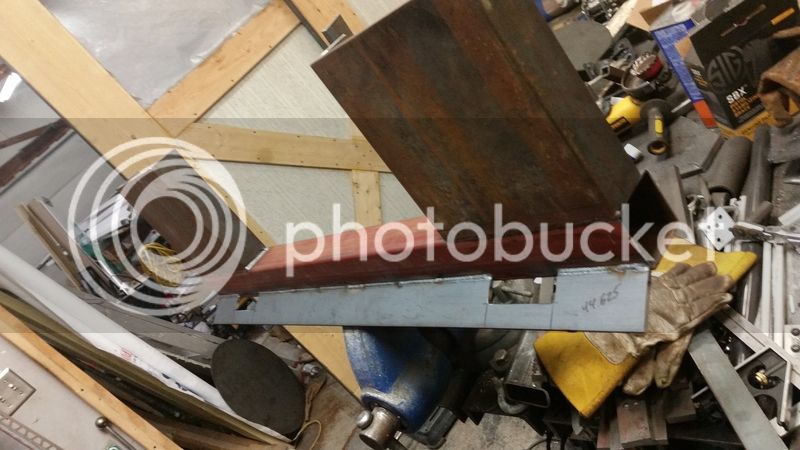
Then today I got more material and continued:
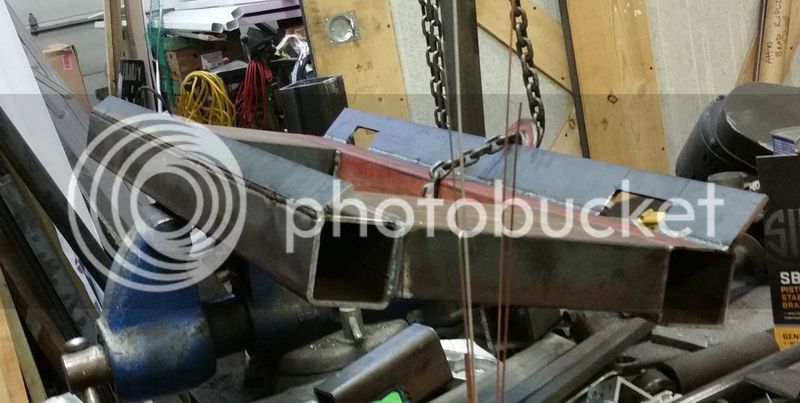
They're not visible in the pics, but I have reinforcement bars welded under the latch tabs on the bottom flange. I used 1/4" for this and the bottom flange on my fork carriage, but the forks don't really put much strain on that connection. The grinder will be fighting to get off the QA mount, so I beefed it up a bit more. I'll also be gusseting those pockets from below as well.
Dinner break, and back to it...