Jim Timber
5 year old buck +
After much cogitating, and getting down to flow capacity and dual demands on the low flow tractor pump, then looking at the additional crap needed to run another pump off the PTO, I decided that Foggy's right and the hydraulic front mount shredder is a no-go.
So Sunday I dropped a wad on Surplus Center and got a 83hp rotary cutter gearbox after confirming with Omni's engineer that the vent just needed to be plugged for use in the horizontal position - and that stuff showed up Wed.
Yesterday I started working on the hub for the gear box:
Then did a triple pass weld on the back (to limit heat input given the splines) and zipped up the front:
Today I got more materials for the 3pt side of things, and trued up the flange on the hub, and then cut the mating surface on the wheel:
Used my super high-tech GreyMatterCAD system to test my layout theory:
Then did some math and drilled a bunch of holes:
I should've moved the inner most cutter over a couple more degrees, but they fit fine.
My right hand started spasming while I was doing the last 3 holes for the pockets. I finished those out despite it probably not being the best idea to keep going. Then stopped for the night, short the 6 mounting bolt holes for the hub flange and a clean up pass to true up the disk. Oh well, I'm pretty satisfied with where I am.
And Foggy, if you get a chance, could you measure the frame to gearbox input shaft length on your grinder for me? I'm not positive on that dimension for mine yet.
So Sunday I dropped a wad on Surplus Center and got a 83hp rotary cutter gearbox after confirming with Omni's engineer that the vent just needed to be plugged for use in the horizontal position - and that stuff showed up Wed.
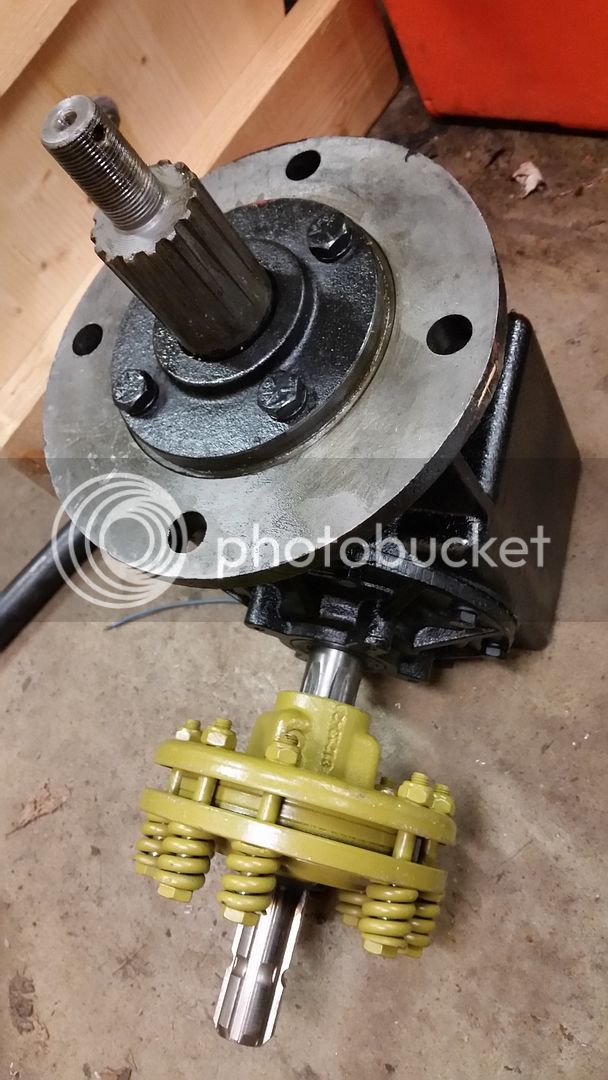
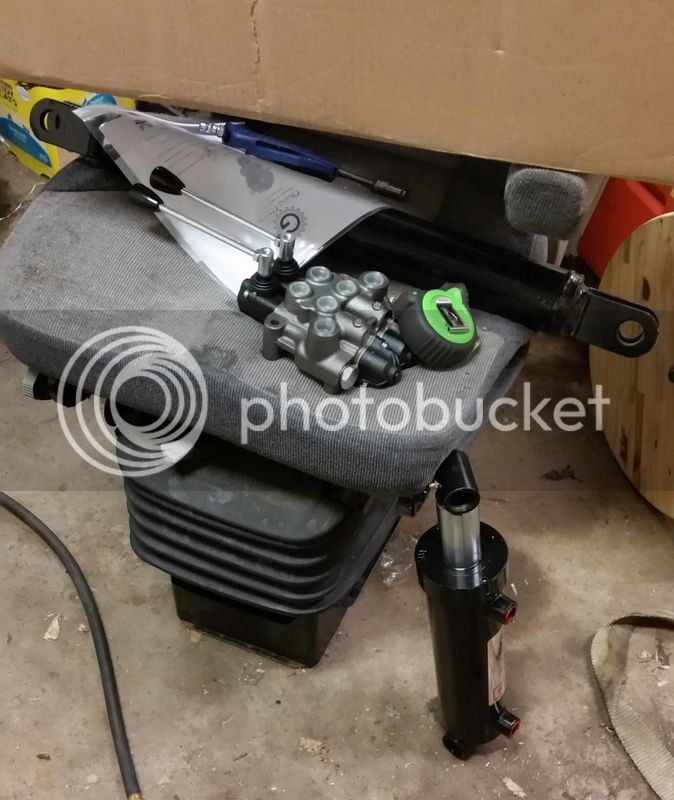
Yesterday I started working on the hub for the gear box:
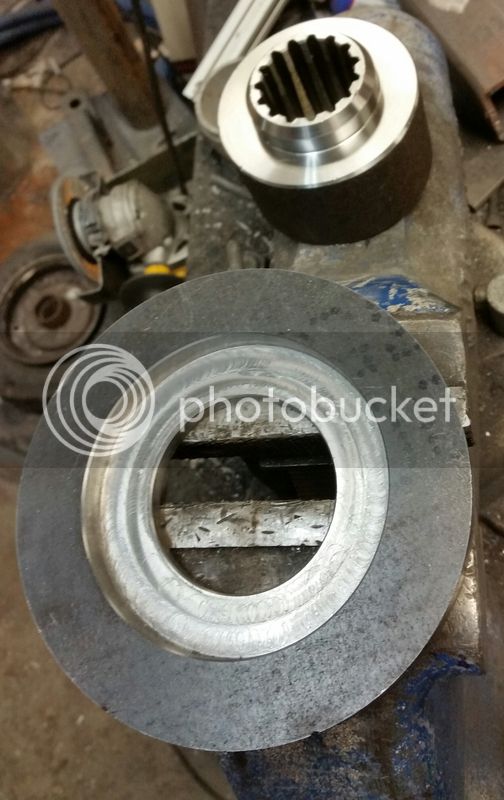
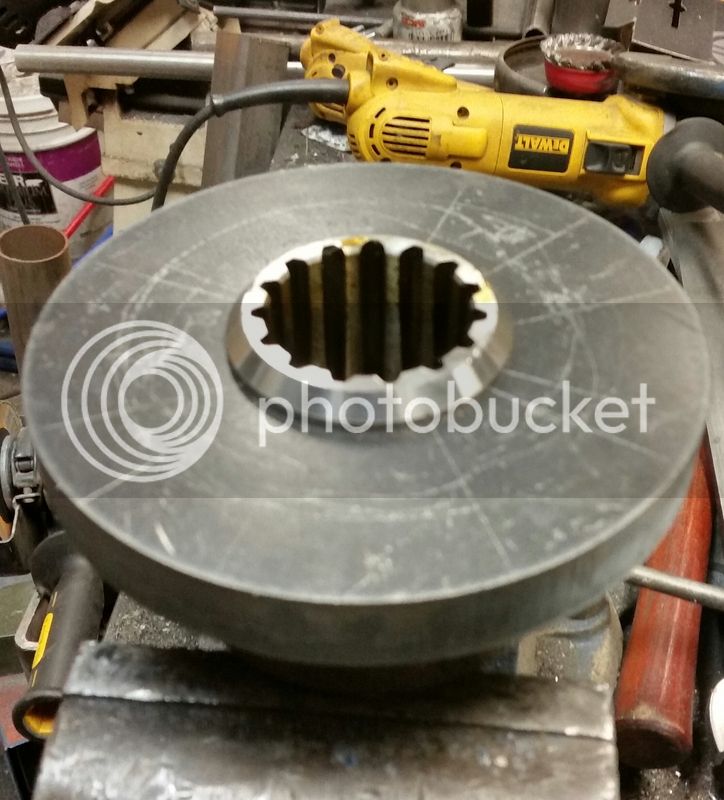
Then did a triple pass weld on the back (to limit heat input given the splines) and zipped up the front:
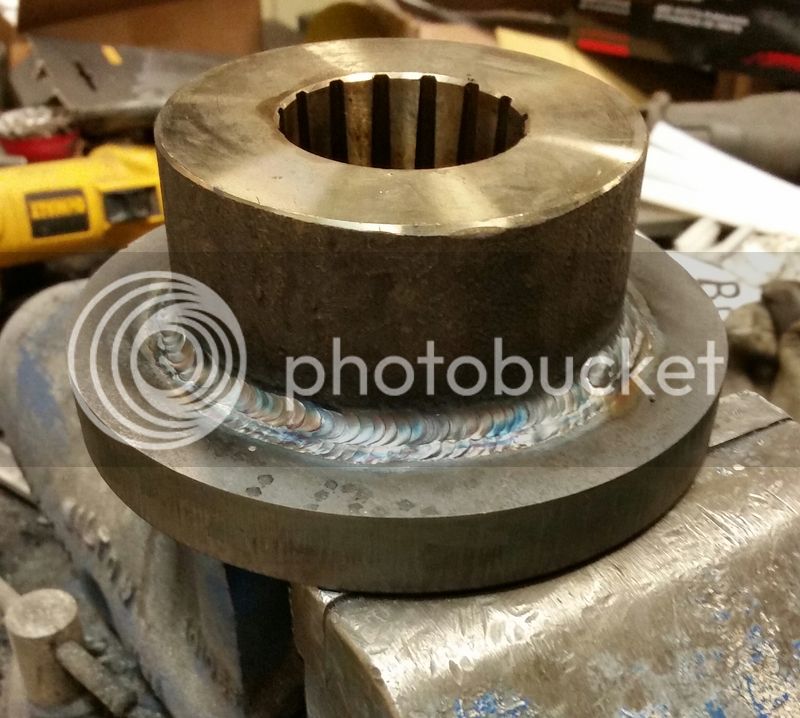
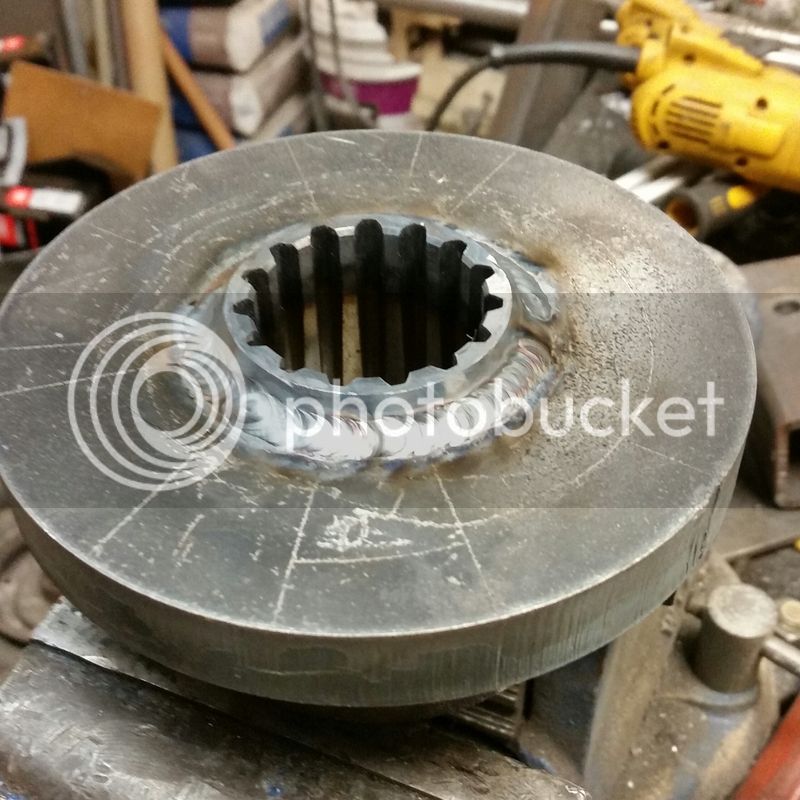
Today I got more materials for the 3pt side of things, and trued up the flange on the hub, and then cut the mating surface on the wheel:
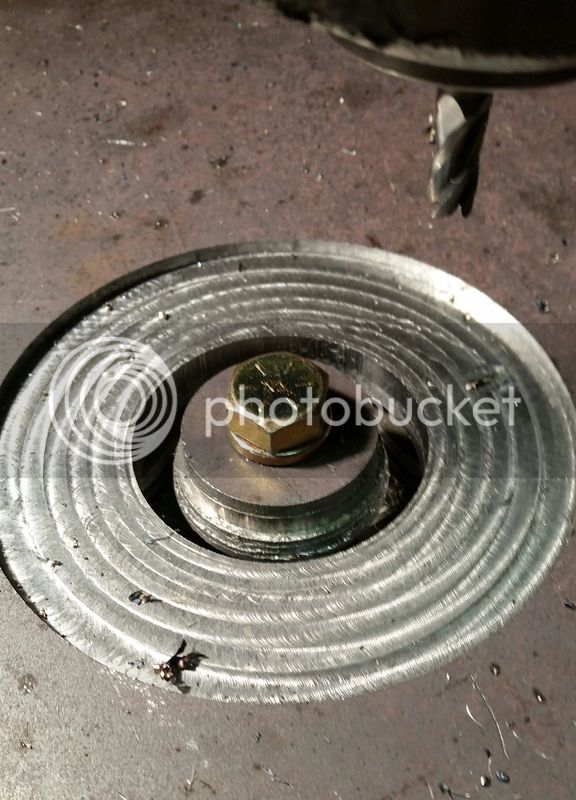
Used my super high-tech GreyMatterCAD system to test my layout theory:
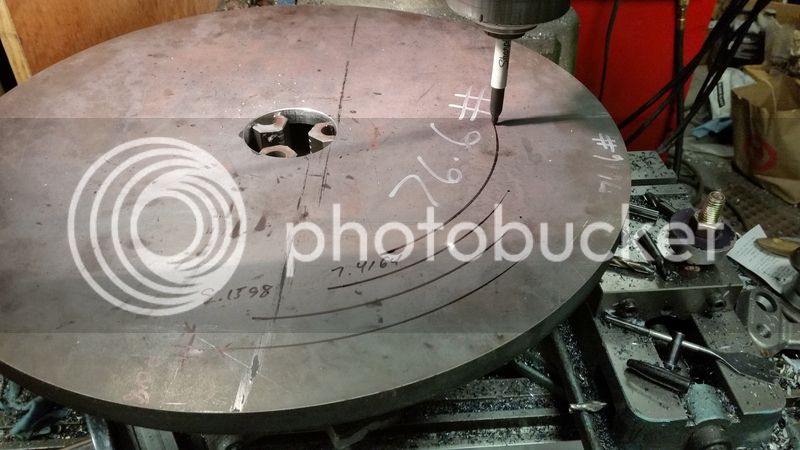
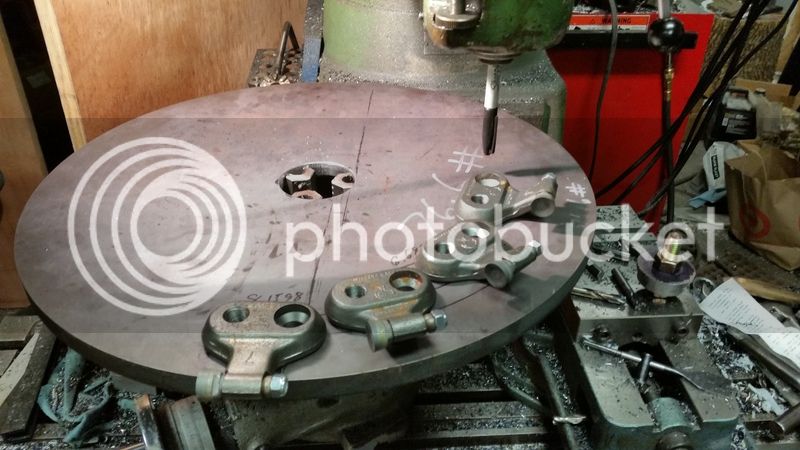
Then did some math and drilled a bunch of holes:
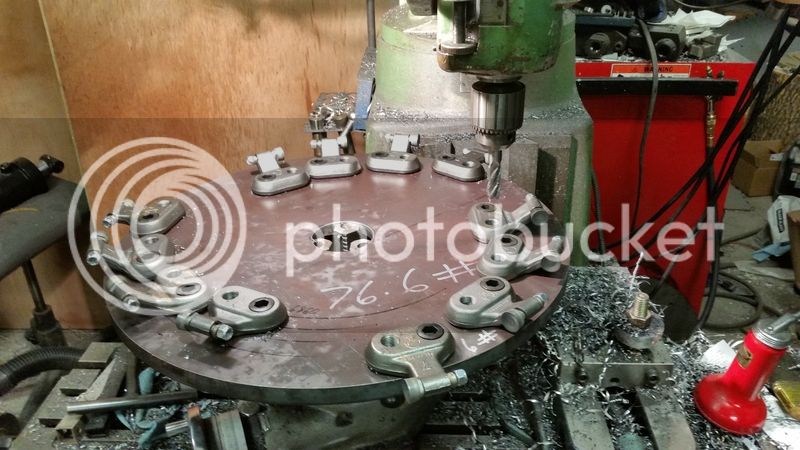
I should've moved the inner most cutter over a couple more degrees, but they fit fine.
My right hand started spasming while I was doing the last 3 holes for the pockets. I finished those out despite it probably not being the best idea to keep going. Then stopped for the night, short the 6 mounting bolt holes for the hub flange and a clean up pass to true up the disk. Oh well, I'm pretty satisfied with where I am.
And Foggy, if you get a chance, could you measure the frame to gearbox input shaft length on your grinder for me? I'm not positive on that dimension for mine yet.