tooln
5 year old buck +
A while back I was asked to build a set of knives for a forum member. These are to be gifts for his son's. When asked if he wanted update along the way he replied he wouldn't mind if I posted them here. At this time he will remain anonymous unless he wants to say otherwise. Through text messages and pictures we worked out the blade profile, finish, handle material etc... There was one concern about the handle size. I wanted everyone to be happy and make sure the knife was going to be comfortable for them. So I made a template from some HDPE that I use & mailed it to him. End result after getting the template was to make the handle 1/2" longer. Sine I had made 2 exact templates I used the spare to trace out the blade and sectioned in 1/2". With Dr., dentist appointment and a planned mini vacation, next week I'll start on the blades. 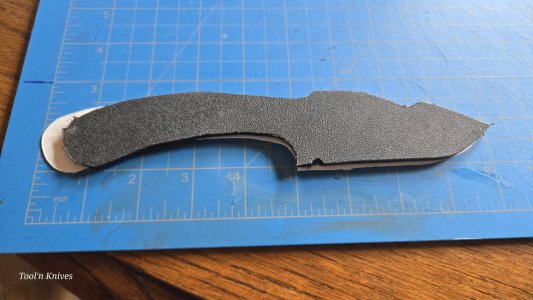
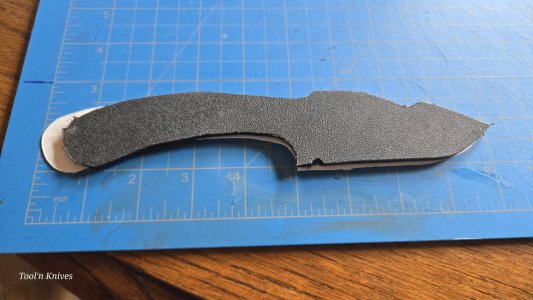